Speaker Breakup and how to reduce its distortion
Introduction
Loudspeakers, despite their crucial role in sound reproduction, can introduce unwanted distortion.
One significant contributor is cone breakup, a phenomenon related to the moving material (diaphragm, cone…) resonance at high frequencies.
This article dives deeper into the science behind cone break-up, its impact on sound quality, and explores filtering techniques to mitigate this issue.
What is speaker break-up?
1. Basic operation
When a speaker emits sound, the voice coil, driven by the signal from the amplifier, moves. Since it is attached to the membrane (cone driver) or a diaphragm (compression driver), it pulls the radiating surface along in its movement.
There are three stages of membrane behavior as frequency increases: pistonic motion, non-pistonic motion, and breakup modes — the latter being a more severe form of non-pistonic behavior characterized by modal resonance patterns across the membrane materials.
At low frequencies, the membrane or cone driver moves uniformly in a pistonic motion.
2. Transition from pistonic to non-pistonic motion
As frequency rises, the radiating surface size becomes comparable to the wavelength, causing phase differences across the surface that lead to a progressive narrowing of directivity.
This geometric effect alone occurs even if the membrane behaves like a perfectly rigid piston.
Simultaneously, material properties induce internal wave propagation delays and localized resonances,
which affect the membrane’s motion and sound distortion but have a secondary influence on directivity compared to the geometric factor.
These phase shifts between the membrane center (driven by the voice coil) and its edges cause the motion to deviate from pure pistonic behavior,
marking the onset of non-pistonic motion. However, this stage does not yet involve breakup or fractionation.
3. Breakup modes and material implications
Breakup modes (or fractionation) arise at higher frequencies, when parts of the radiating surface resonate independently, forming complex modal patterns that depend on the material properties of the membrane.
This results in distortion and irregular radiation distinct from the earlier smooth non-pistonic behavior.
To delay the onset of fractionation, manufacturers can opt for more rigid membranes. However, an ultra-rigid membrane is not ideal, as it introduces internal vibrational modes, also known as modal resonances.
At certain frequencies, these modes cause localized resonances across the surface of the membrane, where different parts vibrate inconsistently, generating undesirable distortions.
Fractionation is inevitable because it is inherent to the shape and material of the membrane.
However, a more rigid membrane will fractionate at higher frequencies and with greater intensity, while also generating more internal vibrational modes, which can contribute to additional distortion.
4. Material strategies and special cases
This is why cone speaker designers often use composite materials and blends to construct membranes, the goal is to strike a balance between rigidity, damping, and weight.
Rigidity pushes fractionation to higher frequencies, while damping reduces the energy of internal resonances, thereby limiting distortion and resonance peaks caused by vibrational modes.
For compression drivers, the diaphragm is usually smaller, and its breakup typically occurs outside the ear’s sensitive range, so it’s less of a problem.
Causes of Cone Break-Up
Cone break-up occurs when the loudspeaker cone resonates at high frequencies, causing it to vibrate in unwanted ways beyond its intended pistonic motion. Several factors influence this resonance:
-
Dimensions, Thickness, and Shape of the Cone:
The size, thickness, and curvature of the cone significantly impact its resonant behavior. Thinner or flatter cones tend to break up earlier than rigid or curved ones. -
Cone Material:
Different materials possess varying stiffness and damping properties. Stiffer materials like metals are more prone to break-up, while materials with inherent damping, like treated paper or composites, can help reduce it. -
Boundary Conditions of the Cone:
How the cone is secured to the frame (suspension) also plays a role. A flexible suspension allows for a wider range of motion before break-up occurs, while a stiffer suspension might limit total excursion but could lead to earlier break-up at specific frequencies.
Impact of Cone Break-Up on Distortion
When the cone breaks up, it generates standing waves that distort the original audio signal.
These distortions manifest as harmonic distortion, perceived as a coloration or harshness in the sound, a H3 distortion at 1khz, so create by a 1khz signal alone, will create sound at 3khz (3 times fundamental).
When a violent break-up occurs at 1500Hz, we have a H3 rise-up at 500Hz (1500/3), so even if we cut at 1kHz we will have the distortion associated to the break-up in the signal and when we will play 500hz we will have an unwanted signal at 1500Hz.
Breakup will also bring Time-domain problems and – for compression drivers – out of plane wave radiation behavior, expecially visible with compression drivers in horns.
Cone Break-Up and Electrical Current
The speaker cone is a mechanical system. When it encounters its resonant frequency, it tends to vibrate in uncontrolled ways – this is cone break-up.
This uncontrolled motion is related to the electrical current flowing through the voice coil.
As the cone vibrates, it generates a back electromotive force (EMF) that opposes the current flow and creates current distortion in the voice coil.
Inductance and Impedance
An inductor opposes changes in current flow. When you increase the inductance in the circuit (like the inherent self-inductance of the voice coil or by adding an external inductor), the overall impedance of the circuit also increases.
Impedance acts like electrical resistance for AC signals like audio.
How Increased Inductance Helps
Here’s how increased inductance tackles cone break-up:
-
Limits Current Flow at Resonance: At the cone’s resonant frequency, the back EMF from the uncontrolled vibration is strongest. The increased inductance makes it harder for the current to rise significantly at this frequency. This reduces the electrical energy delivered to the voice coil, thereby lessening the uncontrolled movement of the cone.
-
Partial Damping Effect: Though not a traditional damping mechanism, the increased opposition to current changes caused by the inductance can have a damping effect. This helps to suppress the excessive vibration of the cone at resonance.
However, it’s important to consider these points:
-
Limited Effect: Increased inductance alone might not entirely eliminate cone break-up, especially for severe break-up issues. It’s often a contributing factor in conjunction with other design elements like cone material and suspension.
-
Frequency Dependence: The impedance increase due to inductance is most significant at higher frequencies. So, the effectiveness in mitigating break-up depends on the resonant frequency of the cone relative to the desired operating range of the woofer.
Filtering Techniques for Break-Up Reduction
Several filtering techniques can be employed to address cone break-up and reduce associated distortion.
As it’s based on impedance rise-up, an EQ in DSP will not have an impact.
The result depends on the woofer’s motor, but it mainly impacts the H3 in most cases. It depends on the design of the motor, the voice coil, and the inductance value. The lower and more linear it is, the less current distortion and distortion in the midrange occur (i.e., a plateau distortion not linked to excursion), which explains why a notch filter has no effect on the distortion of compression drivers, tweeters, and other speakers such as 18Sound AIC speakers.
It’s important to note that these filtering techniques are most effective when the break-up rise up in frequency (one or more big peaks) and/or when woofer is rising up in his final box. If the breakup is already damped, so more or less flat and the woofer has already a flat response in box, it will useless to try something about it.
Each with its advantages and limitations:
Notch Filters
These passive filters use a combination of inductors (L) and capacitors (C) to create a high impedance at the resonant frequency. This effectively reduces the current flow at that frequency, minimizing cone excitation.
However, precise tuning is crucial, and if certain components are placed in parallel with the circuit, this will bypass the impedance effect and make the notch effect on breakup distortion ineffective. So it will work well in conjunction with active filtering, less in passive filtering.
Here is the H3 of a Dayton RS52 with and without LC notch :

Air core inductors with active filtering
These first-order filters, in series, often implemented with a single inductor, allow lower frequencies to pass through while attenuating higher frequencies, including those near the break-up point. This approach offers a simpler design and also linearize the woofer, it’s the easier solution.
It will increase gradually the impedance and replace some EQ to linearize the woofer in the same time, it works very well if the woofer is already rising up in his final box.
The inductor must be an air core inductor and not an iron core inductor; otherwise, it will add H3 distortion in the low end.
Here is the H3 of a SbAcoustics WO24P with and without air inductor in serie :
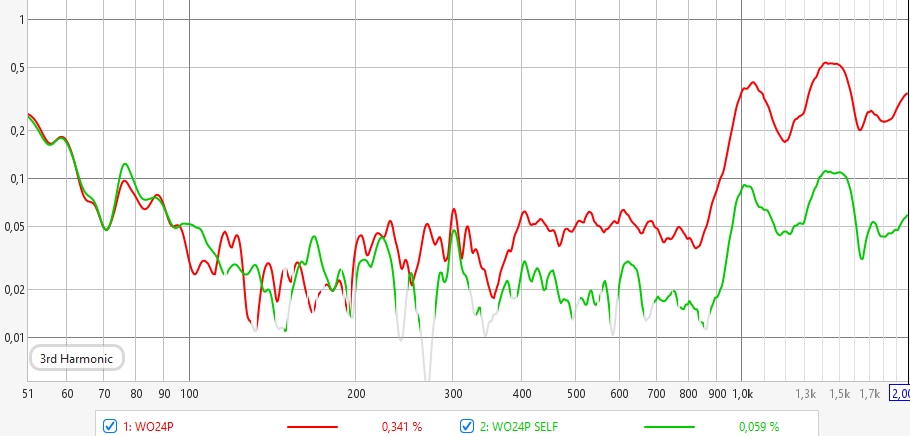
Compensation Networks
More complex networks can be designed to address specific break-up modes. These may involve additional components and require detailed analysis of the cone’s behavior.
Self Inductance
While not a filter in the traditional sense, the inherent self-inductance of the voice coil can also contribute to a rise in impedance at higher frequencies.
This can have a similar effect to filtering, potentially mitigating break-up to some extent.
However, it’s often a secondary effect and may not be sufficient for significant break-up control.
Conclusion
Cone break-up is a significant factor in loudspeaker distortion, impacting sound quality.
By understanding its causes and employing targeted filtering techniques like notch filters or high-pass filters, speaker designers can achieve smoother, more accurate sound reproduction.